INTERVIEW先輩社員インタビュー
様々な現場で働く先輩社員たちに
本音を語ってもらいました。
溶接が製品の品質を左右します
仕上がりにこだわるのは仕事を面白くするため
金属加工メーカーの技術の差は、最終的に製品のどこに現れるかと言いますと「溶接の付け根」なんです。そこが製品でいちばん弱いところです。溶接で手抜きがあったり不備があると溶接の付け根から亀裂が入って割れたり、もろくなったりいろんな不具合が出ます。だから溶接は製品にとって大切な工程です。当社では、社内資格やJIS資格、その他の資格が必要で、溶接箇所や内容によっては会社から認定された社員でないとできません。いまベアチューブを溶接できるのは6人、スリーブ溶接は私ひとりです。
溶接の技術とは、見た目のキレイさと欠陥の有無で決まります。溶接跡が一定で、左右が均等、図面上の「のど厚」に合っているかなどの項目を確認して認定をもらいます。
認定資格は必要なものですが、自分が納得できる溶接かどうかを大切にしています。光沢や色、不純物が浮いていないか、などです。そういう仕上がりの良さにこだわるのは、仕事を面白くするためでもあります。いったん妥協すればどこまでも妥協してしまうし、それでは仕事が楽しくないでしょう。
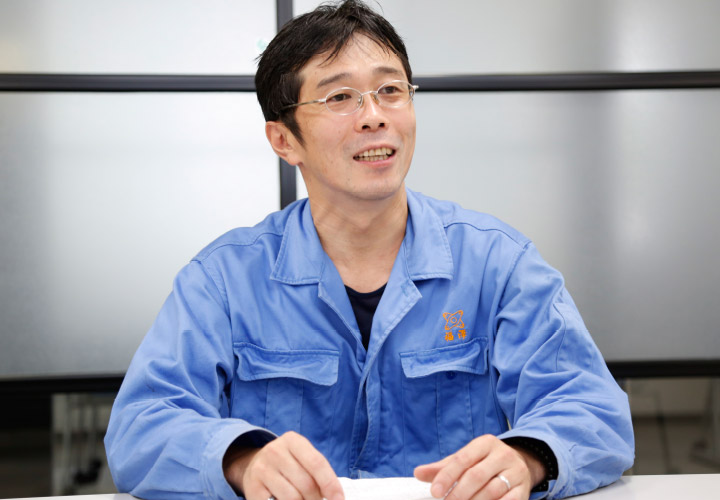
数をこなせば感覚が研ぎ澄まされます
音だけで溶接の出来がわかります
溶接の部署に来てはじめの段階は真っ直ぐ走らせる練習をします。その次はビード、これは溶接した箇所の盛り上がり部分のことですが、その高さを揃えることが求められます。非破壊検査、破壊試験で溶接技術をパスしたあとは、溶接の姿勢です。工場内だけではなく現地で溶接できるか。全ての姿勢で溶接できるか、右手左手どちらでもできるか。そういうテストを受けます。なぜそんなテストがあるのかと言えば、この箇所の溶接は下向きで行いなさい、と姿勢まで指定されているからです。それと、どの姿勢でも出来ないと、製品を動かして溶接することになります。大きな製品なら人手も要りますし、納期も遅れます。入社した頃はスマホも動画もなく、先輩に教えてもらい、何度もやり直して腕を磨いていきました。先輩の仕事を数多く目で見て、耳を澄ませ、気づかないうちに感覚が研ぎ澄まされたように思います。そうなると目で見なくても音で溶接の出来不出来がわかるようになります。若い人がバチ、バチバチ、バチと不安定な音を出していると、これはあかんな、となります(笑)。やはり数をこなすことが大切だと思います。私もいつのまにか後輩に教える立場になりましたが、上達は人それぞれ。器用でない人も苦手な子も数をこなせばできるようになります。
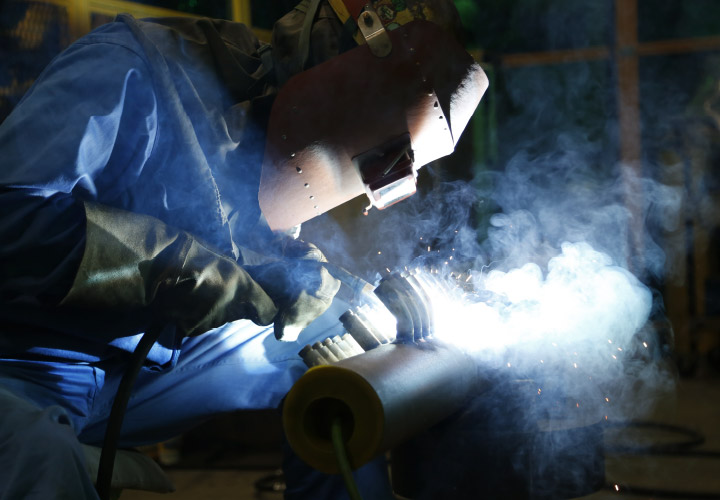
ロボット開発に挑戦
私のこだわりも再現できるようにしたい
この工場では溶接ロボットが稼働しています。数年前に溶接ロボットの開発を会社から言われてスタートしました。ロボットはもちろんまったくの専門外です。他社のロボットを視察するところから始めました。ただ、自分がロボット開発をすることに違和感はありませんでした。求めるものは同じと言うか、溶接の仕上がり、品質が自分で納得がいくようなものを作ればいいと。基礎的な部分は専門の人に作ってもらいましたが、プログラムの講習を受けに行ってあとは自分でコツコツと細部を詰めていきました。普段、自分が溶接しているときの手の角度を測ったり、スピードや音も再現できるような調整です。
なんども試作品を作って、試験に合格しOKが出ています。製品としては問題ありません。あとは、仕上がりの色とか、私のこだわりの部分ですね。ゆくゆくは、部材を動かす作業もロボット化したいと考えています。

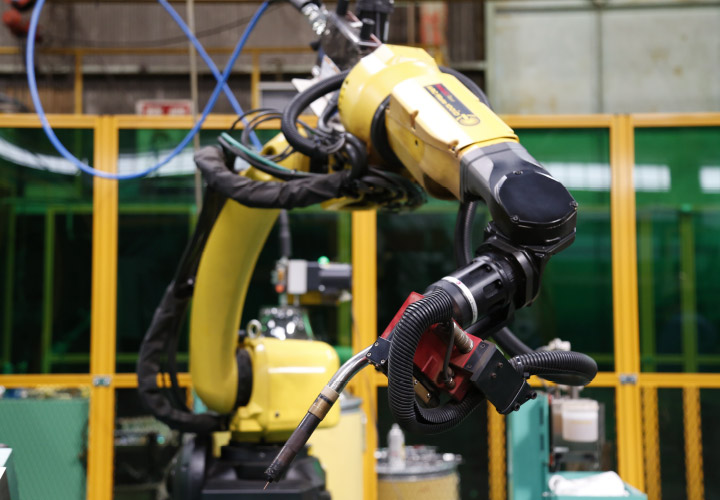
interview02
福澤 祥光三日市工場 工作 1995年入社
溶接一筋25年。速さと美しさを兼ね備えた溶接技術は社内トップクラスと絶大な信頼を得ている。これを読む人にひと言、とお願いすると「若いうちにいろいろ経験してみて自分に合うもの、人に負けないものを見つける。それを磨けばいいと思います」。